ام دی اف (MDF) یا تخته فیبر با چگالی متوسط (Medium Density Fiberboard)، یک محصول چوبی مهندسی شده است که از تجزیه بقایای چوب سخت یا نرم به الیاف چوب، اغلب در یک دفیبریتور، ترکیب آن با موم و یک چسب رزین و تشکیل پنلها با استفاده از دمای بالا و فشار ساخته میشود. این فرآورده معمولاً از تخته سهلا متراکمتر است. از الیاف جدا شده تشکیل شده است، اما میتواند به عنوان یک مصالح ساختمانی مشابه با کاربرد تخته سهلا استفاده شود همچنین قویتر و بسیار متراکمتر از تخته نئوپان است.
چندین تصور غلط در مورد این تختهها وجود دارد و اغلب با تخته سهلا و تختههای فیبر اشتباه گرفته میشوند. یک تخته MDF مخفف تخته فیبر با چگالی متوسط است و بیشتر به عنوان جایگزین چوب در نظر گرفته میشود و به عنوان یک ماده مفید برای محصولات تزئینی و همچنین مبلمان خانگی مورد استفاده قرار میگیرد.
اگر با این چوب آشنا نیستید، ما در این مقاله قصد داریم تا شما را بیشتر با آن آشنا کنیم و شما را با نحوه ساخت و استفاده از آنها آشنا سازیم.
مواد تشکیل دهنده ام دی اف (MDF)
این تختههای پرکاربرد با تجزیه چوب سخت و نرم به الیاف چوب ساخته میشود. صفحات ام دی اف معمولا از ۸۲٪ فیبر چوب، ۹٪ چسب رزین اوره-فرمالدئید، ۸٪ آب و ۱٪ موم پارافین تشکیل شده است.
چگالی آن معمولاً بین ۵۰۰ کیلوگرم بر متر مکعب (۳۱ پوند بر فوت مکعب) تا ۱۰۰۰ کیلوگرم بر متر مکعب (۶۲ پوند بر فوت مکعب) است. محدوده چگالی و طبقهبندی این صفحات به عنوان تخته سبک، استاندارد یا با چگالی بالا، یک نامگذاری نادرست و گیجکننده است.
چگالی تخته هنگام ارزیابی نسبت به چگالی فیبری که برای ساخت پنل استفاده میشود، مهم است. یک پنل ام دی اف ضخیم با چگالی ۷۰۰-۷۲۰ کیلوگرم بر متر مکعب ممکن است در مورد پانلهای فیبر با چوب نرم به عنوان چگالی بالا در نظر گرفته شود، در حالی که یک پنل با همان چگالی ساخته شده از الیاف چوب سخت به این صورت در نظر گرفته نمیشود.
فرآیند تولیدام دی اف (MDF)
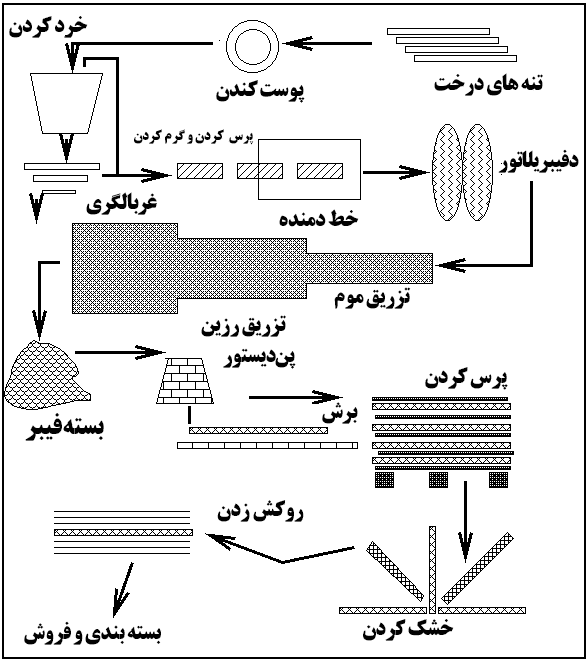
مراحل تولید ام دی اف
مواد خام مورد استفاده برای تولید یک قطعه ام دی اف باید قبل از مناسب شدن برای استفاده، از فرآیند خاصی عبور کنند. از یک آهنربای بزرگ برای حذف هرگونه ناخالصی مغناطیسی استفاده میشود و مواد بر اساس اندازه جدا میشوند. سپس مواد فشرده میشوند تا آب آنها خارج شود و سپس توسط یک ریزکننده آنها را به قطعات کوچک خرد میکنند.
سپس برای ایجاد چسبندگی در الیاف از رزین استفاده میشود. بعد از این مرحله، مخلوط حاصله در یک خشککن بسیار بزرگ قرار میگیرد که با گاز یا روغن گرم میشود. این ترکیب خشک از یک کمپرسور استوانه ای شکل که مجهز به کنترلهای کامپیوتری میباشد، عبور میکند تا تراکم و استحکام مناسب را بدست آورد. قطعات حاصل سپس در حالی که هنوز گرم هستند با اره صنعتی به اندازه صحیح برش داده میشوند.
الیاف به صورت جداگانه و دستنخورده، به عنوان الیاف و رگچههای منفرد پردازش میشوند و از طریق یک فرآیند خشک تولید میشوند. سپس تراشههای چوب با استفاده از یک فیدر مارپیچی به پلاگهای کوچک فشرده میشوند، به مدت ۳۰ تا ۱۲۰ ثانیه حرارت داده میشوند تا لیگنین چوب نرم شود و سپس به یک دستگاه دفیبریتور تغذیه میشوند. یک دفیبریتور معمولی شامل دو دیسک چرخان در جهت مخالف هم است که در سطح خود شیارهایی دارند.
تراشههای چوب به مرکز دستگاه تغذیه میشوند و با نیروی گریز از مرکز به سمت خارج بین دیسک ها هدایت میشوند. اندازه شیارها به تدریج رو به کاهش مییابدو این کاهش اندازه، به همراه لیگنین نرم شده بین الیاف، به جداسازی الیاف کمک میکند.
از دفیبریلاتور، خمیر چوب وارد یک “خط دمنده” میشود که بخش متمایزی از فرآیند MDF است. این یک خط لوله دایرهای گسترشیافته است که در ابتدا قطر آن 40 میلیمتر است و به 1500 میلیمتر افزایش مییابد. موم در مرحله اول تزریق میشود که الیاف را میپوشاند و به طور یکنواخت توسط حرکت آشفته الیاف توزیع میشود.
سپس رزین اوره-فرمالدئید به عنوان عامل چسب اصلی تزریق میشود. موم مقاومت در برابر رطوبت را بهبود میبخشد و رزین در ابتدا به کاهش چسبندگی کمک میکند. مواد در محفظه انبساط نهایی گرم شده خط دمشی به سرعت خشک میشود و به یک الیاف ریز، کرکی و سبک تبدیل میشود. این الیاف ممکن است بلافاصله استفاده شود یا ذخیره شود.
فرآیند شکلدهی ورق MDF
فیبر خشک به بالای یک “پندیستور” مکیده میشود که الیاف را به طور یکنواخت در یک تشک یکنواخت با ضخامت معمولاً ۲۳۰-۶۱۰ میلیمتر توزیع میکند. تشک پیشفشرده شده و یا مستقیماً به یک پرس گرم پیوسته یا به ورقهای بزرگ برای یک پرس گرم چند دهانه برش داده میشود. پرس گرم رزین چسب را فعال میکند و مشخصات استحکام و چگالی را تنظیم میکند.
چرخه پرس در مراحل انجام میشود، ابتدا ضخامت تشک به حدود ۱.۵ برابر ضخامت تخته نهایی فشرده میشود، سپس در مراحل بعدی بیشتر فشرده میشود و برای مدت کوتاهی نگه داشته میشود. این یک پروفایل تخته با مناطق چگالی افزایش یافته و در نتیجه استحکام مکانیکی، نزدیک به دو سطح تخته و یک هسته کمتر متراکم ایجاد میکند.
پس از پرس، MDF در یک خشککن ستارهای یا چرخ فلکه خنککننده خنک میشود، برش داده شده و سنباده زده میشود. در برخی کاربردها، تختهها نیز برای استحکام بیشتر لمینت میشوند.
موارد استفاده از چوب MDF
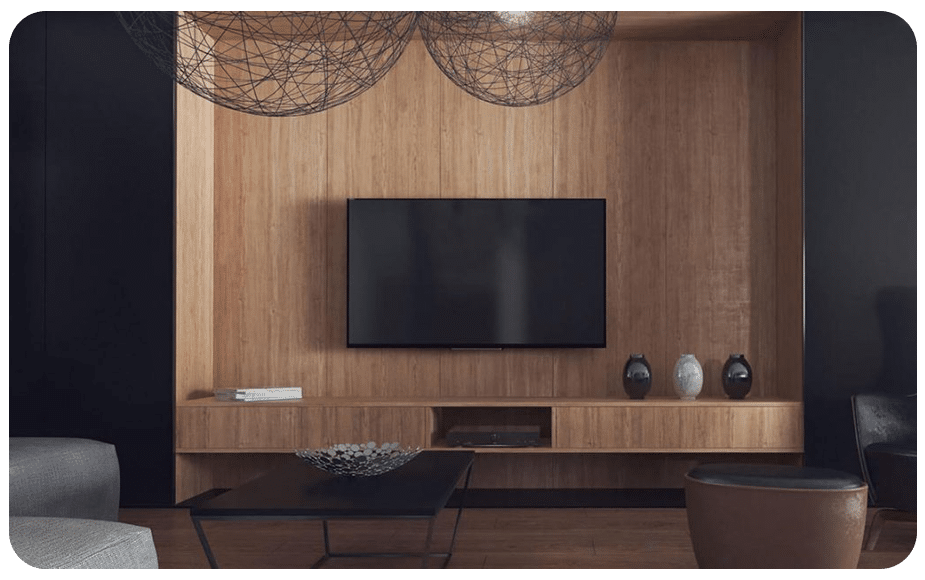
کاربرد ام دی اف mdf
چوب MDF (Medium Density Fiberboard) به دلیل خواص منحصر به فردی که دارد، کاربردهای بسیار گستردهای در صنایع مختلف پیدا کرده است. از جمله مهمترین موارد استفاده از MDF میتوان به موارد زیر اشاره کرد:
در صنعت مبلمان و دکوراسیون داخلی:
- کابینت آشپزخانه: به دلیل مقاومت در برابر رطوبت، تنوع رنگ و طرح، و قابلیت برش آسان، MDF یکی از محبوبترین گزینهها برای ساخت کابینت آشپزخانه است.
- کمد دیواری: ساخت کمدهای دیواری با MDF به دلیل وزن کم، استحکام بالا و قابلیت نصب انواع روکشها، بسیار رایج است.
- قفسه و کتابخانه: MDF به دلیل سطح صاف و یکنواخت، برای ساخت قفسهها و کتابخانههای با طراحی متنوع بسیار مناسب است.
- میز و صندلی: ساخت میز و صندلی با MDF به دلیل قابلیت شکلدهی آسان و تنوع رنگ، بسیار محبوب است.
- سرویس خواب: MDF در ساخت تخت خواب، پاتختی و سایر اجزای سرویس خواب نیز کاربرد فراوانی دارد.
در صنعت ساختمانی:
- درب داخلی: MDF به دلیل عایق صدا و حرارت بودن، برای ساخت دربهای داخلی بسیار مناسب است.
- پارتیشن: ساخت پارتیشنهای داخلی با MDF به دلیل وزن کم و قابلیت نصب آسان، بسیار رایج است.
- روکش دیوار: MDF با روکشهای مختلف، برای پوشش دیوارها و ایجاد طرحهای متنوع به کار میرود.
سایر کاربردها:
- صنعت خودرو: در ساخت داشبورد و برخی قطعات داخلی خودرو استفاده میشود.
- صنعت بستهبندی: برای ساخت قفسههای نمایشگاهی، جعبهها و سایر محصولات بستهبندی استفاده میشود.
- صنعت تبلیغات: برای ساخت تابلوهای تبلیغاتی و نمایشگاهی استفاده میشود.
مزایای استفاده از ام دی اف(MDF)
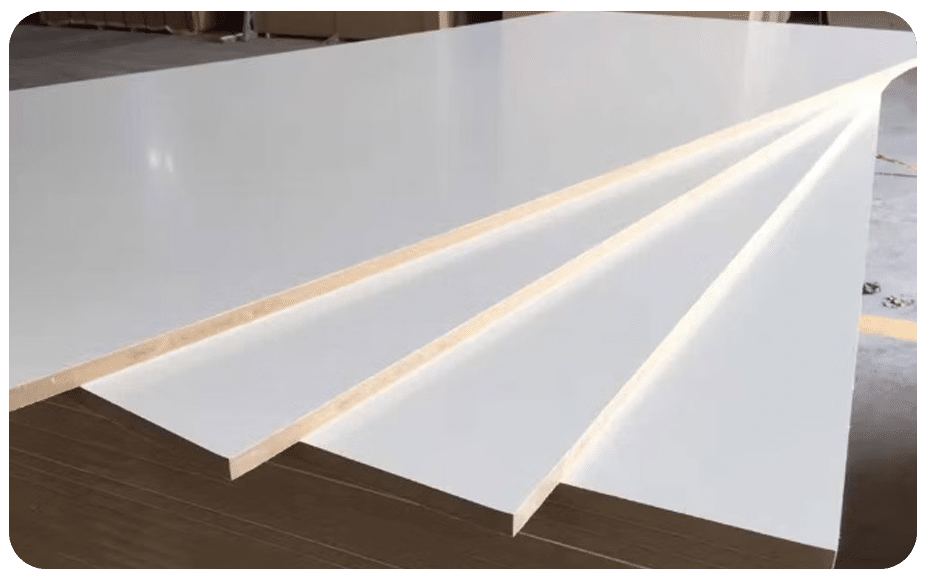
چوب ام دی اف
- قیمت مناسب: نسبت به چوب طبیعی، قیمت MDF بسیار مناسبتر است.
- وزن کم: وزن کمی دارد و حمل و نقل آن آسان است.
- استحکام بالا: استحکام بالایی دارد و در برابر ضربه مقاوم است.
- قابلیت شکلدهی آسان: MDF را میتوان به راحتی برش، سوراخکاری و خم کرد.
- تنوع رنگ و طرح: این فرآورده در انواع رنگها و طرحها موجود است و قابلیت روکش شدن با انواع مواد را دارد.
- عایق صدا و حرارت: این تختهها عایق صدا و حرارت خوبی است.
معایب استفاده از ام دی اف(MDF)
- مقاومت کم در برابر رطوبت: این محصول در برابر رطوبت زیاد مقاومت کمی دارد و ممکن است متورم شود.
- مقاومت کم در برابر حرارت زیاد: این تختهها در برابر حرارت زیاد مقاومت کمی دارد و ممکن است بسوزد.
- وجود فرمالدئید: برخی از انواع MDF حاوی فرمالدئید هستند که ممکن است برای سلامتی مضر باشد.
نکته: برای استفاده از MDF در محیطهای مرطوب یا مکانهایی که در معرض حرارت زیاد هستند، باید از انواع مقاوم در برابر رطوبت و حرارت استفاده شود. همچنین، بهتر است از MDFهایی استفاده شود که میزان فرمالدئید آنها کم باشد.
مراحل تولید در یک نگاه:
- آمادهسازی مواد اولیه:
- انتخاب و آمادهسازی چوبهای مناسب
- خرد کردن چوب به تراشههای کوچک
- جدا کردن ناخالصیها و ذرات فلزی
- تولید خمیر چوب:
- نرم کردن تراشههای چوب با حرارت و بخار
- استفاده از دفیبریتور برای جدا کردن الیاف چوب
- افزودن مواد افزودنی:
- اضافه کردن رزین اوره-فرمالدئید به عنوان چسب
- اضافه کردن موم پارافین برای بهبود مقاومت در برابر رطوبت
- شکلدهی ورق:
- پاشیدن مخلوط الیاف و چسب به یک نوار متحرک
- فشردن و گرم کردن نوار برای تشکیل ورق MDF
- خشک کردن و برش:
- خشک کردن ورقهای MDF در خشککنهای مخصوص
- برش ورقها به اندازههای مورد نیاز
- پرداخت نهایی:
- سنبادهزنی و پرداخت سطح ورقها
- لمینیت کردن (در صورت نیاز)
- بستهبندی و توزیع:
- بستهبندی ورقهای MDF و ارسال آنها به بازار